In the granulation industry, whether it is a flat die pellet machine or a ring die pellet machine, its working principle is to rely on the relative movement between the pressure rollershell and the mold to grab the material and enter the effective station, extrude it into shape, and then cut it into particles of the required length by the cutting blade.
Particle press roller shell
The pressure roller shell mainly includes an eccentric shaft, rolling bearings, a pressure roller shell sleeved outside the pressure roller shaft, and components used to support and fix the pressure roller shell.
The pressure rollershell squeezes the material into the mold hole and forms it under pressure in the mold hole. In order to prevent the pressure roller from slipping and increase the gripping force, there must be a certain friction force between the pressure roller and the material. Therefore, measures to increase friction and wear resistance are often taken on the surface of the pressure roller. When the structural parameters of the pressure roller and mold are determined, the structural form and size of the outer surface of the pressure roller have a significant impact on the granulation efficiency and particle quality.
Surface structure of pressure roller shell
There are three common types of surface for the existing particle press rollers: grooved roller surface, grooved roller surface with edge sealing, and honeycomb roller surface.
The toothed groove type pressure roller has good rolling performance and is widely used in livestock and poultry feed factories. However, due to the sliding of feed in the toothed groove, the wear of the pressure roller and ring mold is not very uniform, and the wear at both ends of the pressure roller and ring mold is more severe.
The toothed groove type pressure roller with edge sealing is mainly suitable for the production of aquatic materials. Aquatic materials are more prone to sliding during extrusion. Due to the edge sealing on both sides of the toothed groove, it is not easy to slide towards both sides during feed extrusion, resulting in a more uniform distribution of feed. The wear of the pressure roller and the ring mold is also more uniform, resulting in a more consistent length of the produced pellets.
The advantage of honeycomb roller is that the wear of the ring mold is uniform, and the length of the produced particles is also relatively consistent. However, the performance of the coil is poor, which affects the output of the granulator and is not as common as the use of slot type in actual production.
The following is a summary of 10 types of particle machine pressure rollers for Baoshell pressure roller ring molds, and the last 3 are definitely the ones you haven't seen!
NO.10 Groove type
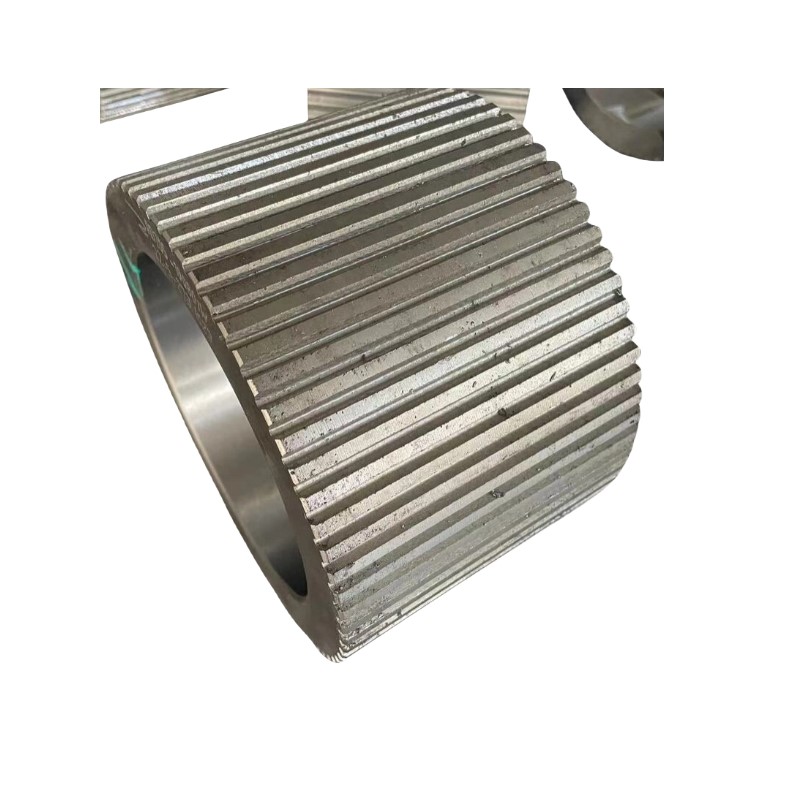
NO.9 Closed groove type
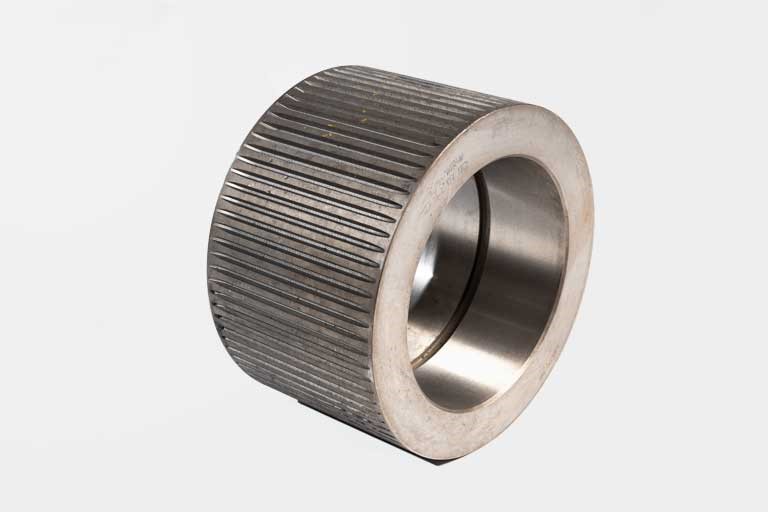
NO.8 Honeycomb type
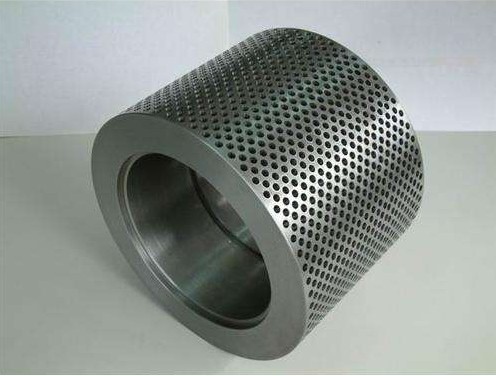
NO.7 Diamond shaped
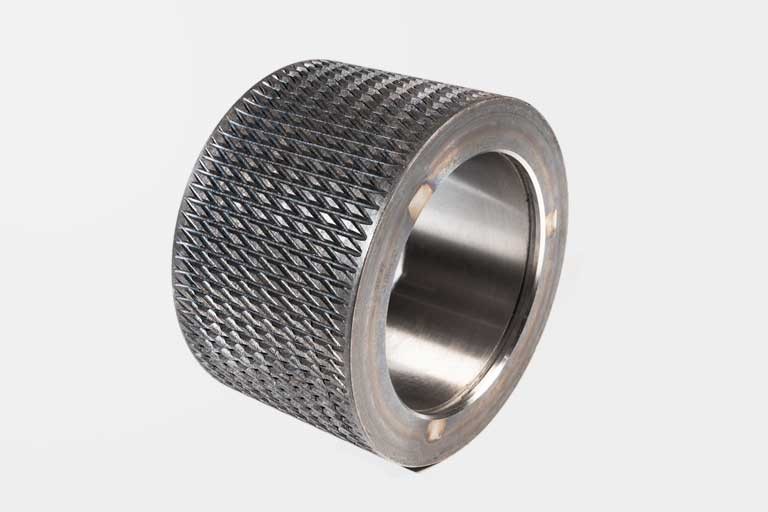
NO.6 Inclined groove
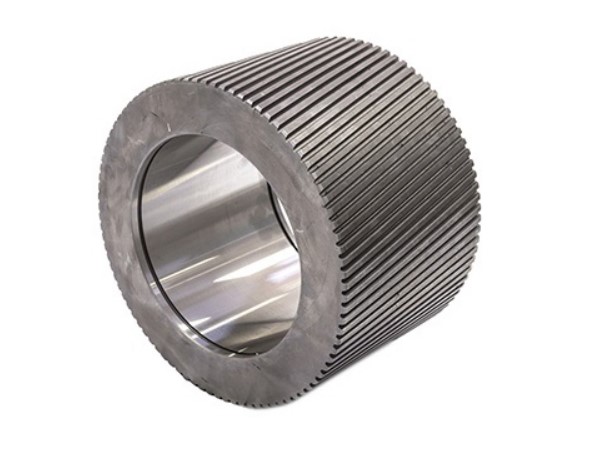
NO.5 Groove+honeycomb
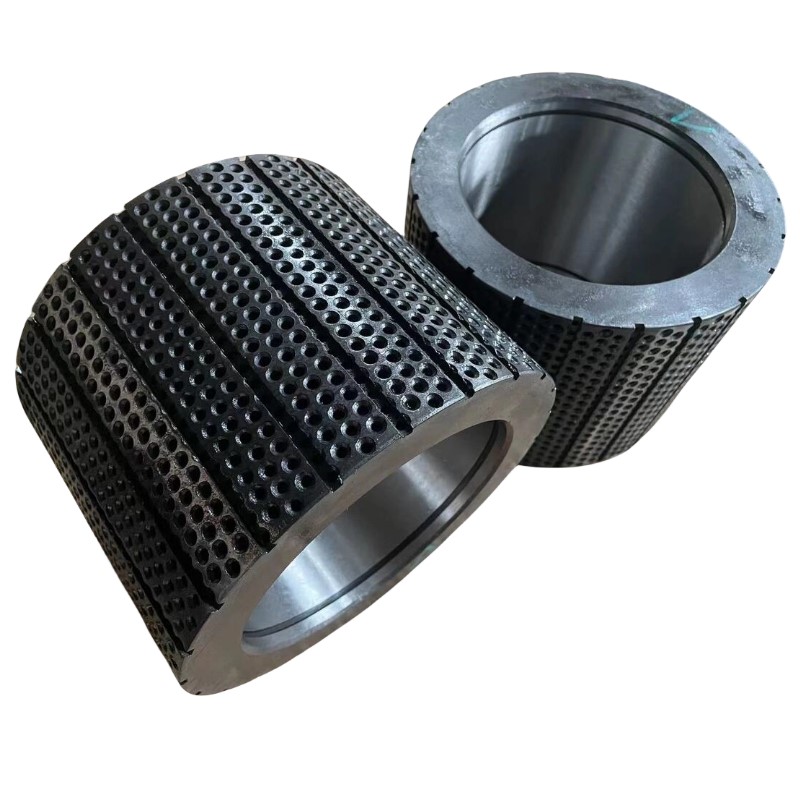
NO.4 Closed groove+honeycomb
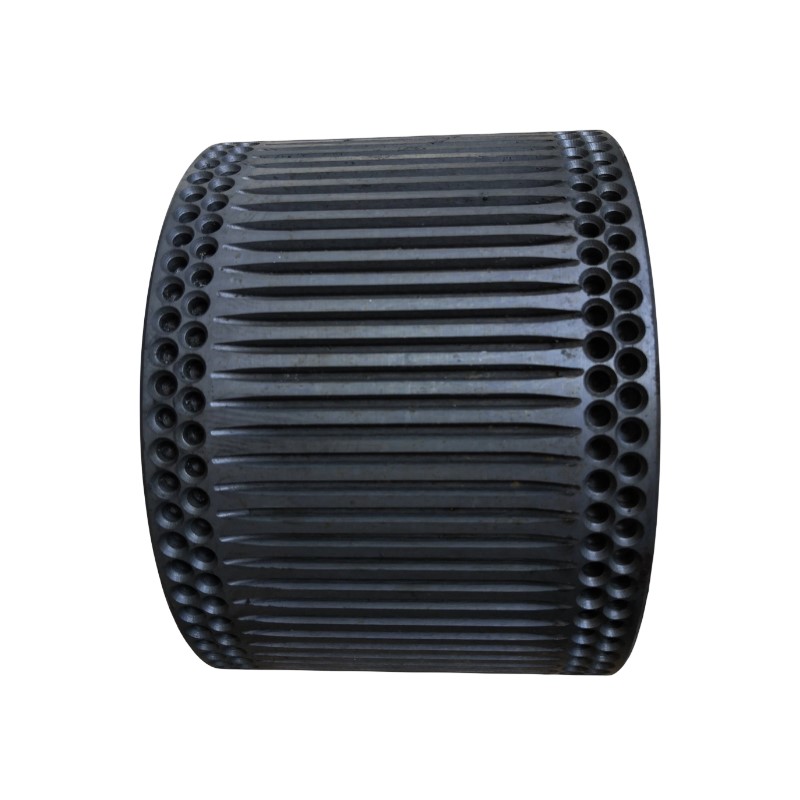
NO.3 Inclined groove+honeycomb
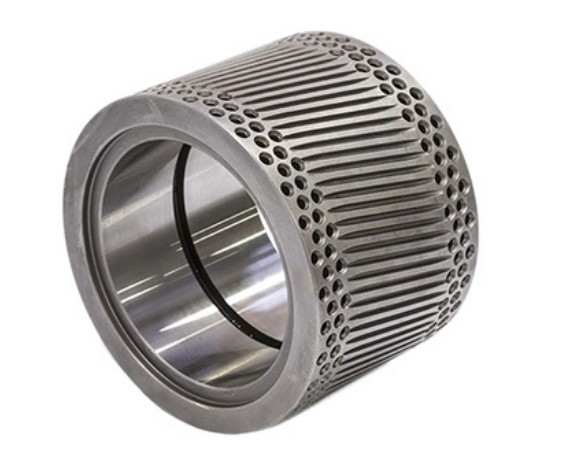
NO.2 Fish bone ripple
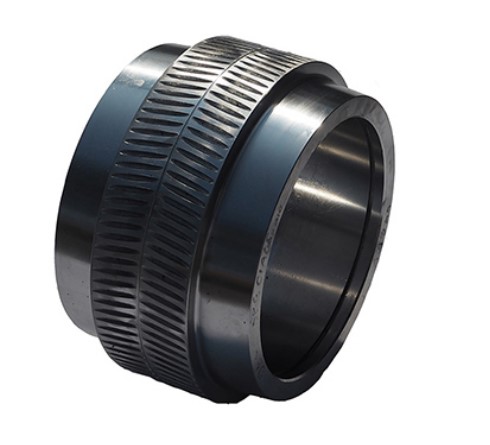
NO.1 Arc-shaped ripple
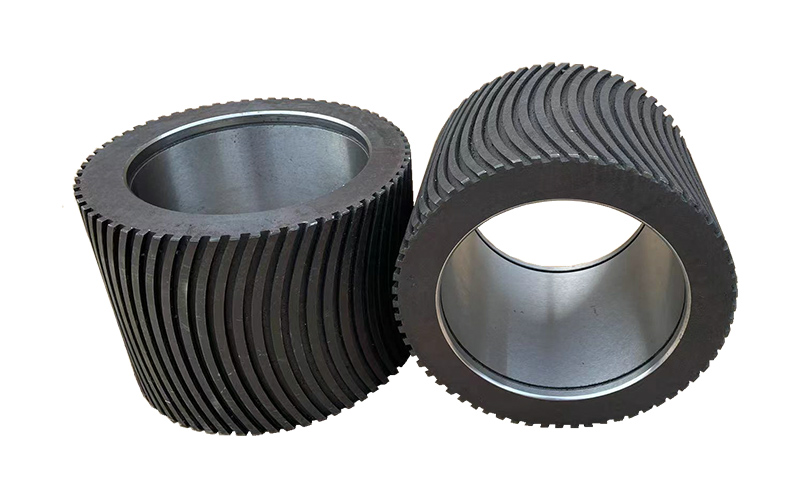
SEPPECIAL MODEL: TUNGSTEN CARBIDE COLLER SHELL
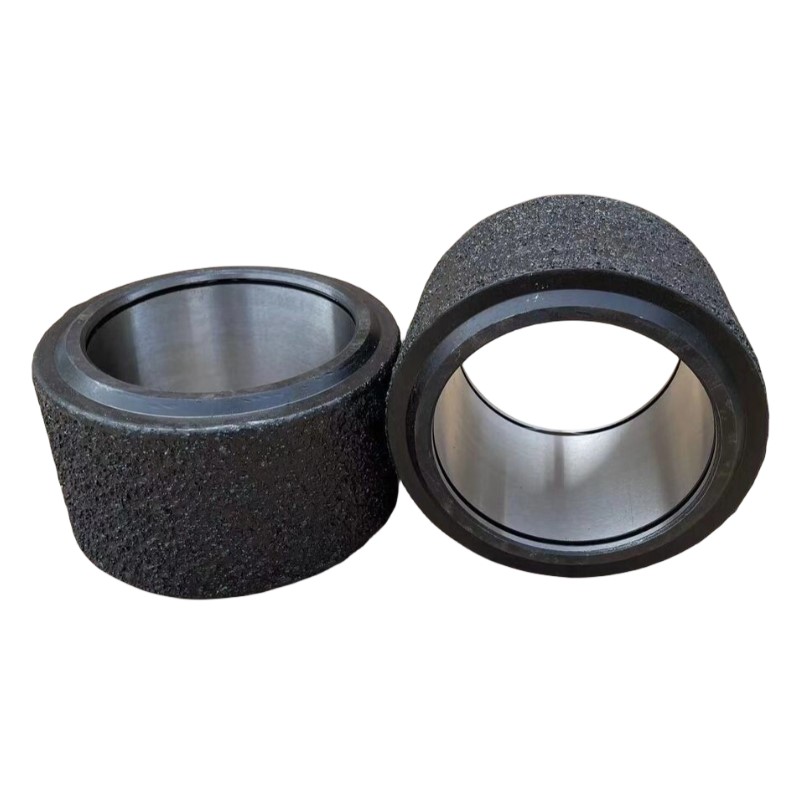
The treatment method for the slipping of the pressure roller of the particle machine
Due to the harsh working environment, high working intensity, and fast wear rate of the pressure roller shell, the pressure roller is a vulnerable part of the particle machine and needs to be replaced regularly. Production practice has shown that as long as the characteristics of the production materials change or other conditions change during the processing, the phenomenon of slipping of the pressure roller of the particle machine may occur. If there is slipping of the pressure roller during the granulation process, please do not panic. For specific details, please refer to the following techniques:
Reason 1: Poor concentricity of the pressure roller and spindle installation
Solution:
Check if the installation of the pressure roller bearings is reasonable to avoid causing the pressure roller shell to deviate to one side.
Reason 2: The bell mouth of the ring mold is ground flat, causing the mold to not eat materials
Solution:
Check the wear of the clamps, transmission wheels, and lining rings of the granulator.
Adjust the concentricity of the ring mold installation, with an error not exceeding 0.3mm.
The gap between the pressure rollers should be adjusted to: half of the working surface of the pressure rollers is working with the mold, and the gap adjustment wheel and locking screw should also be ensured to be in good working condition.
When the pressure roller slips, do not let the particle machine idle for a long time and wait for it to discharge material on its own.
The compression ratio of the ring mold aperture used is too high, which causes high material discharge resistance of the mold and is also one of the reasons for the slipping of the pressure roller.
The pellet machine should not be allowed to idle unnecessarily without material feeding.
Reason 3: The pressure roller bearing is stuck
Solution:
Replace the pressure roller bearings.
Reason 4: The pressure roller shell is not round
Solution:
The quality of the roller shell is unqualified, replace or repair the roller shell.
When the pressure roller slips, it should be stopped in a timely manner to avoid prolonged idle friction of the pressure roller.
Reason 5: Bending or loosening of the pressure roller spindle
Solution:
Replace or tighten the spindle, and check the condition of the pressure roller spindle when replacing the ring mold and pressure roller.
Reason 6: The working surface of the pressure roller is relatively misaligned with the working surface of the ring mold (edge crossing)
Solution:
Check if the pressure roller is installed improperly and replace it.
Check if the eccentric shaft of the pressure roller is deformed.
Check for wear on the main shaft bearings or bushings of the particle machine.
Reason 7: The spindle clearance of the granulator is too large
Solution:
Check the tightening clearance of the granulator.
Reason 8: The punching rate of the ring mold is low (less than 98%)
Solution:
Use a pistol drill to drill through the mold hole, or boil it in oil, grind it before feeding.
Reason 9: Raw materials are too coarse and have high moisture content
Solution:
Pay attention to maintaining a moisture content of about 15%. If the moisture content of the raw materials is too high, there will be mold blockage and slippage after the raw materials enter the ring mold. The moisture control range of the raw materials is between 13-20%.
Reason 10: New mold feeding too fast
Solution:
Adjust the speed to ensure that the pressure roller has sufficient traction, prevent the pressure roller from slipping, and promptly check the wear of the ring mold and pressure roller.
Post time: Mar-25-2024