Due to the lower harmful substances such as ash, nitrogen, and sulfur in biomass compared to mineral energy, it has the characteristics of large reserves, good carbon activity, easy ignition, and high volatile components. Therefore, biomass is a very ideal energy fuel and is very suitable for combustion conversion and utilization. The residual ash after biomass combustion is rich in nutrients required by plants such as phosphorus, calcium, potassium, and magnesium, so it can be used as fertilizer for returning to the field. Given the enormous resource reserves and unique renewable advantages of biomass energy, it is currently regarded as an important choice for national new energy development by countries around the world. The National Development and Reform Commission of China has clearly stated in the "Implementation Plan for Comprehensive Utilization of Crop Straw during the 12th Five Year Plan" that the comprehensive utilization rate of straw will reach 75% by 2013, and strive to exceed 80% by 2015.
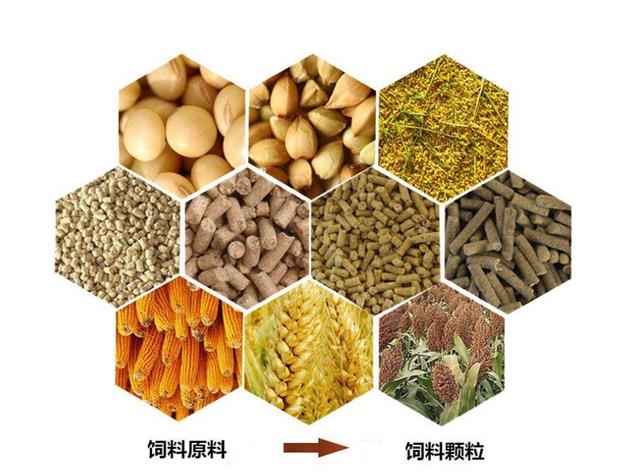
How to convert biomass energy into high-quality, clean, and convenient energy has become an urgent problem to be solved. Biomass densification technology is one of the effective ways to improve the efficiency of biomass energy incineration and facilitate transportation. At present, there are four common types of dense forming equipment in the domestic and foreign markets: spiral extrusion particle machine, piston stamping particle machine, flat mold particle machine, and ring mold particle machine. Among them, the ring mold pellet machine is widely used due to its characteristics such as no need for heating during operation, wide requirements for raw material moisture content (10% to 30%), large single machine output, high compression density, and good forming effect. However, these types of pellet machines generally have disadvantages such as easy mold wear, short service life, high maintenance costs, and inconvenient replacement. In response to the above shortcomings of the ring mold pellet machine, the author has made a brand new improvement design on the structure of the forming mold, and designed a set type forming mold with long service life, low maintenance cost, and convenient maintenance. Meanwhile, this article conducted a mechanical analysis of the forming mold during its working process.
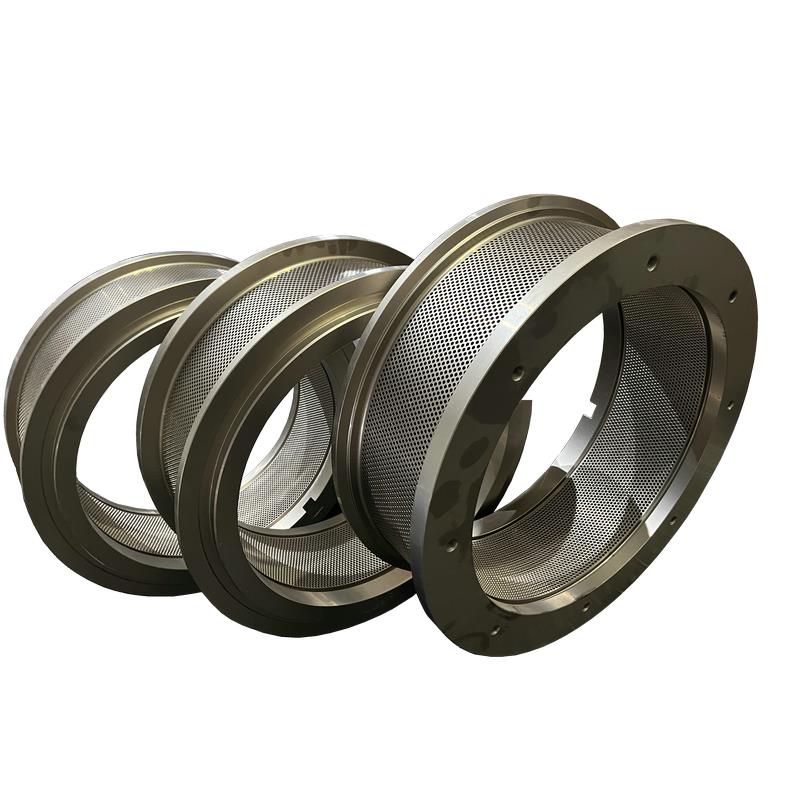
1. Improvement Design of the Forming Mold Structure for Ring Mold Granulator
1.1 Introduction to Extrusion Forming Process: The ring die pellet machine can be divided into two types: vertical and horizontal, depending on the position of the ring die; According to the form of motion, it can be divided into two different forms of motion: the active pressing roller with a fixed ring mold and the active pressing roller with a driven ring mold. This improved design is mainly aimed at the ring mold particle machine with an active pressure roller and a fixed ring mold as the motion form. It mainly consists of two parts: a conveying mechanism and a ring mold particle mechanism. The ring mold and pressure roller are the two core components of the ring mold pellet machine, with many forming mold holes distributed around the ring mold, and the pressure roller is installed inside the ring mold. The pressure roller is connected to the transmission spindle, and the ring mold is installed on a fixed bracket. When the spindle rotates, it drives the pressure roller to rotate. Working principle: Firstly, the conveying mechanism transports the crushed biomass material into a certain particle size (3-5mm) into the compression chamber. Then, the motor drives the main shaft to drive the pressure roller to rotate, and the pressure roller moves at a constant speed to evenly disperse the material between the pressure roller and the ring mold, causing the ring mold to compress and friction with the material, the pressure roller with the material, and the material with the material. During the process of squeezing friction, cellulose and hemicellulose in the material combine with each other. At the same time, the heat generated by squeezing friction softens lignin into a natural binder, which makes cellulose, hemicellulose, and other components more firmly bound together. With the continuous filling of biomass materials, the amount of material subjected to compression and friction in the forming mold holes continues to increase. At the same time, the squeezing force between biomass continues to increase, and it continuously densifies and forms in the molding hole. When the extrusion pressure is greater than the friction force, the biomass being extruded continuously from the molding holes around the ring mold, forming biomass molding fuel with a molding density of about 1g/Cm3.
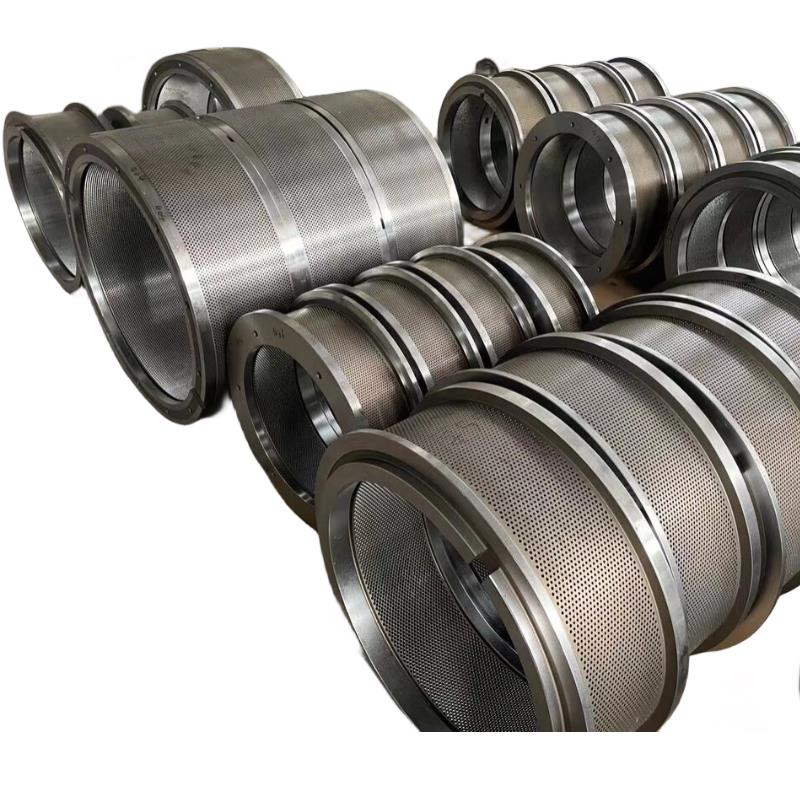
1.2 Wear of Forming Molds: The single machine output of the pellet machine is large, with a relatively high degree of automation and strong adaptability to raw materials. It can be widely used for processing various biomass raw materials, suitable for large-scale production of biomass dense forming fuels, and meeting the development requirements of biomass dense forming fuel industrialization in the future. Therefore, the ring mold pellet machine is widely used. Due to the possible presence of small amounts of sand and other non biomass impurities in the processed biomass material, it is highly likely to cause significant wear and tear on the pellet machine's ring mold. The service life of the ring mold is calculated based on production capacity. Currently, the service life of the ring mold in China is only 100-1000t.
The failure of the ring mold mainly occurs in the following four phenomena: ① After the ring mold works for a period of time, the inner wall of the forming mold hole wears and the aperture increases, resulting in significant deformation of the formed fuel produced; ② The feeding slope of the forming die hole of the ring mold is worn off, resulting in a decrease in the amount of biomass material squeezed into the die hole, a decrease in extrusion pressure, and easy blockage of the forming die hole, leading to the failure of the ring mold (Figure 2); ③ After the inner wall materials and sharply reduces the discharge amount (Figure 3);
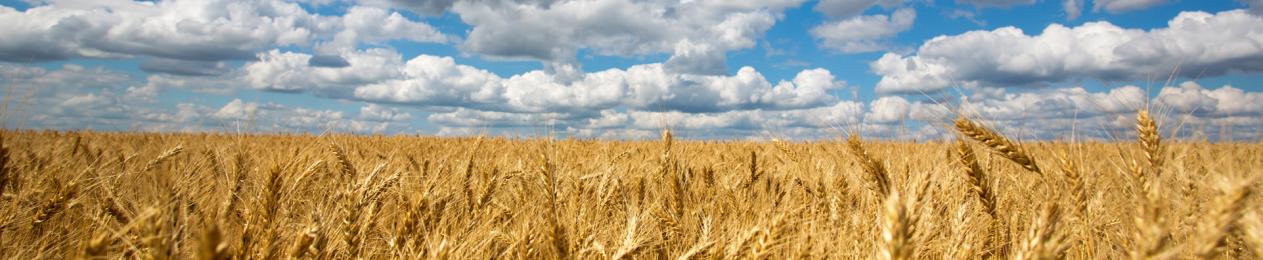
④ After the wear of the inner hole of the ring mold, the wall thickness between adjacent mold pieces L becomes thinner, resulting in a decrease in the structural strength of the ring mold. Cracks are prone to occur in the most dangerous section, and as the cracks continue to extend, the phenomenon of ring mold fracture occurs. The main reason for the easy wear and short service life of the ring mold is the unreasonable structure of the forming ring mold (the ring mold is integrated with the forming mold holes). The integrated structure of the two is prone to such results: sometimes when only a few forming mold holes of the ring mold are worn out and cannot work, the entire ring mold needs to be replaced, which not only brings inconvenience to the replacement work, but also causes great economic waste and increases maintenance costs.
1.3 Structural Improvement Design of Forming Mold In order to extend the service life of the ring mold of the pellet machine, reduce wear, facilitate replacement, and reduce maintenance costs, it is necessary to carry out a brand new improvement design on the structure of the ring mold. The embedded molding mold was used in the design, and the improved compression chamber structure is shown in Figure 4. Figure 5 shows the cross-sectional view of the improved molding mold.
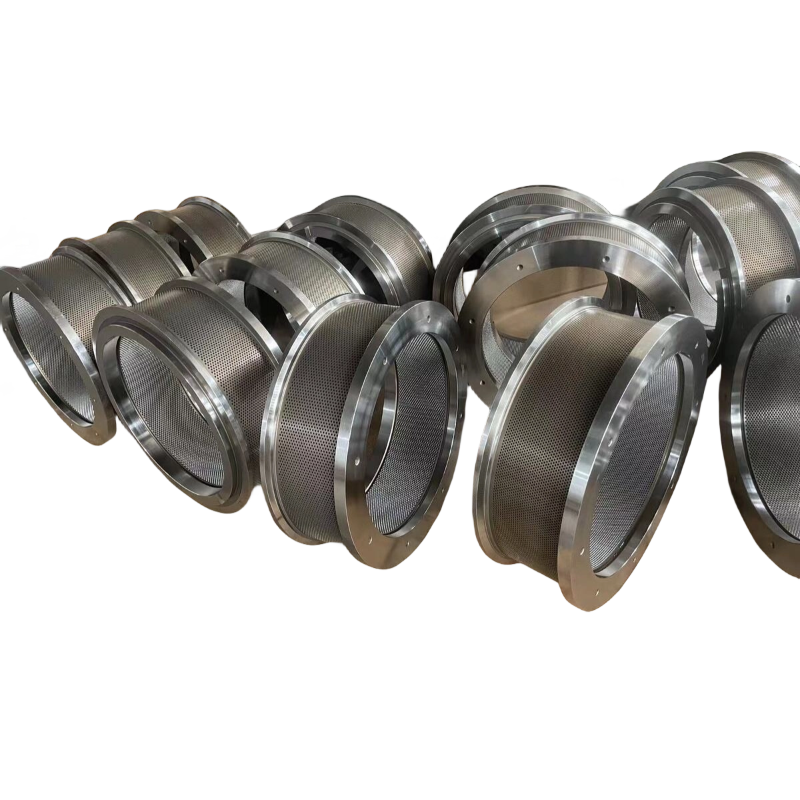
This improved design is mainly aimed at the ring mold particle machine with a motion form of active pressure roller and fixed ring mold. The lower ring mold is fixed on the body, and the two pressure rollers are connected to the main shaft through a connecting plate. The forming mold is embedded on the lower ring mold (using interference fit), and the upper ring mold is fixed on the lower ring mold through bolts and clamped onto the forming mold. At the same time, in order to prevent the forming mold from rebounding due to force after the pressure roller rolls over and moving radially along the ring mold, countersunk screws are used to fix the forming mold to the upper and lower ring molds respectively. In order to reduce the resistance of the material entering the hole and make it more convenient to enter the mold hole. The conical angle of the feeding hole of the designed forming mold is 60 ° to 120 °.
The improved structural design of the forming mold has the characteristics of multi cycle and long service life. When the particle machine works for a period of time, friction loss causes the aperture of the forming mold to become larger and passivated. When the worn forming mold is removed and expanded, it can be used for the production of other specifications of forming particles. This can achieve the reuse of molds and save maintenance and replacement costs.
In order to extend the service life of the granulator and reduce production costs, the pressure roller adopts high carbon high manganese steel with good wear resistance, such as 65Mn. The forming mold should be made of alloy carburized steel or low-carbon nickel chromium alloy, such as containing Cr, Mn, Ti, etc. Due to the improvement of the compression chamber, the friction force experienced by the upper and lower ring molds during operation is relatively small compared to the forming mold. Therefore, ordinary carbon steel, such as 45 steel, can be used as the material for the compression chamber. Compared to traditional integrated forming ring molds, it can reduce the use of expensive alloy steel, thereby lowering production costs.
2. Mechanical analysis of the forming mold of the ring mold pellet machine during the working process of the forming mold.
During the molding process, the lignin in the material is completely softened due to the high-pressure and high-temperature environment generated in the molding mold. When the extrusion pressure is not increasing, the material undergoes plasticization. The material flows well after plasticization, so the length can be set to d. The forming mold is regarded as a pressure vessel, and the stress on the forming mold is simplified.
Through the above mechanical calculation analysis, it can be concluded that in order to obtain the pressure at any point inside the forming mold, it is necessary to determine the circumferential strain at that point inside the forming mold. Then, the frictional force and pressure at that location can be calculated.
3. Conclusion
This article proposes a new structural improvement design for the forming mold of the ring mold pelletizer. The use of embedded forming molds can effectively reduce mold wear, extend mold cycle life, facilitate replacement and maintenance, and reduce production costs. At the same time, mechanical analysis was conducted on the forming mold during its working process, providing a theoretical basis for further research in the future.
Post time: Feb-22-2024